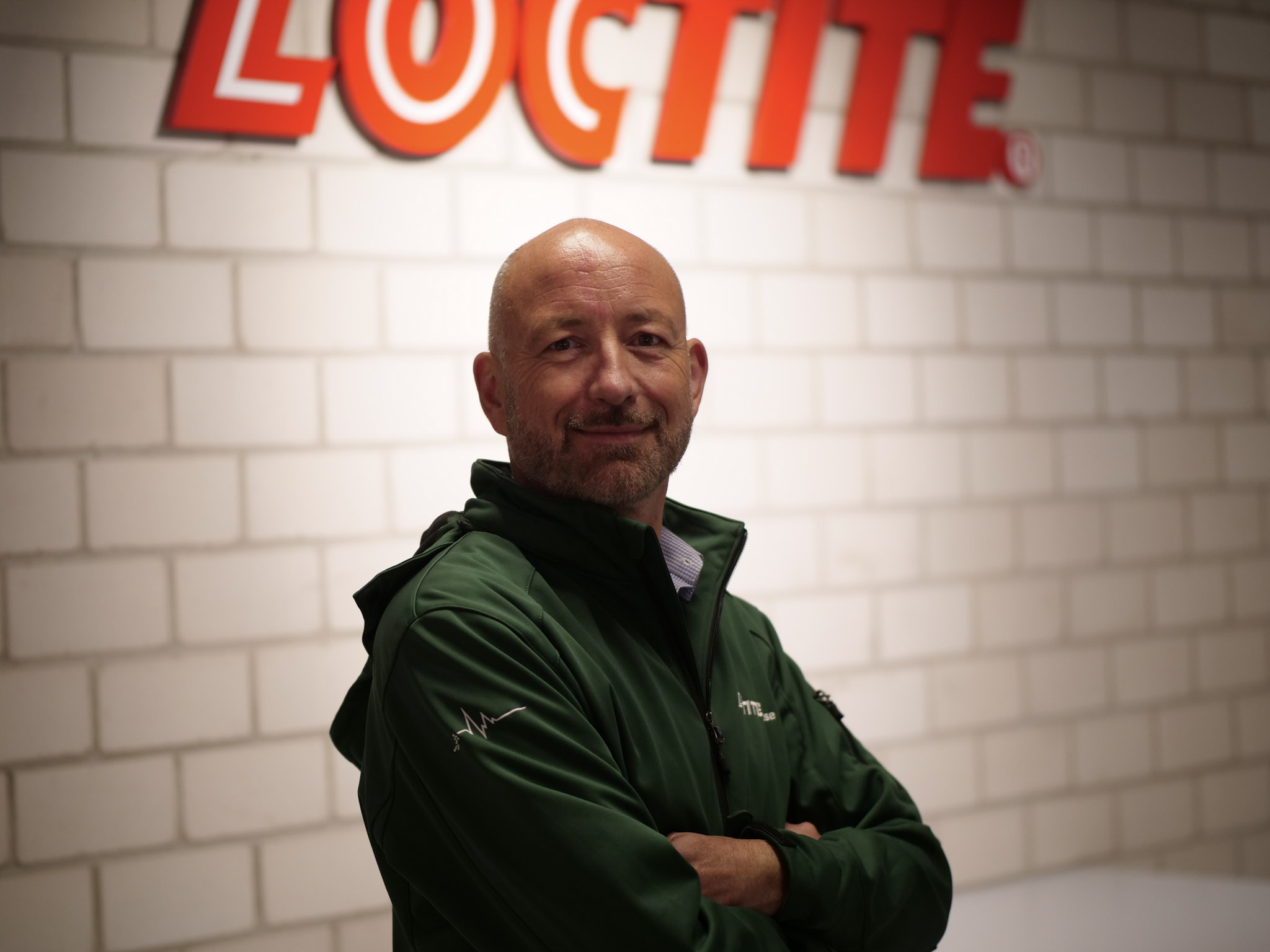
« À terme, Henkel souhaite devenir le leader mondial dans les domaines de la maintenance industrielle et de la maintenance 4.0 »
Nouveau membre au niveau national de l’AFIM, Henkel est très connu du grand public pour ses nombreux produits du quotidien présents chez 84% des foyers français. Pourtant, le groupe réalise la moitié de son chiffre d’affaires dans les adhésifs techniques (activité pour laquelle il est le n°1 mondial), et une grande partie en maintenance. C’est d’ailleurs dans ce domaine que le groupe entend bien s’imposer avec des solutions qui dépassent le spectre de la réparation avec des technologies connectées. Le point avec David Mouginot, Business Developer LOCTITE Pulse, solutions de maintenance 4.0 et spécialise depuis de nombreuses années de l’adhésif.
Que représente le groupe Henkel en France et dans le monde ?
David Mouginot
Henkel est un groupe composé de plus de 50 000 employés dont un millier de personnes en France, bien connu du grand public à travers sa division « Consumer Brands » et de ses grandes marques de soins capillaires, lessives, détergents, nettoyants… Mais il est également le leader mondial des adhésifs, notamment des adhésifs techniques (produits d’étanchéité et de revêtement) pour l’industrie, activité qui représente 50 % de son chiffre d’affaires, soit 11,2 Md€ (et 11 Md€ pour la division Consumer brands), et qui a signé en 2022 une croissance de 13,2 %. Baptisée « Adhesive Technologies », cette division rassemble les colles, les mastics, les lubrifiants, les nettoyants et autres composites pour le renforcement structurel, sans oublier les nouveaux capteurs digitaux 4.0.
Quelle est votre actualité, en particulier dans l’Hexagone ?
David Mouginot
Henkel France est en train de déménager son nouveau siège à Metal 57, Boulogne-Billancourt (dans les anciens ateliers de Renault) où il réunira à partir de janvier prochain les deux activités de la filiale française. Mais notre actualité concerne davantage le renforcement de notre position dans la maintenance industrielle et notamment le MRO 4.0, des domaines dans lesquels on ambitionne d’être le leader, grâce au récent rachat du groupe américain CRITICA Infrastructure, connu pour sa marque de composites CSNRI. Car si Henkel est historiquement reconnu dans la maintenance des sites industriels grâce à notre gamme de colles anaérobies LOCTITE (les bouteilles rouges qui se trouvent dans tous les ateliers de maintenance pour des freinage de filetage, de l’étanchéité filetée), le groupe offre en réalité une gamme bien plus large de solutions...
En quoi consiste ce positionnement du point de vue solutions technologiques ?
David Mouginot
Le MRO 4.0 passe inévitablement par les capteurs. Ceux-ci se révèlent aujourd'hui indispensables dans la mesure où l’on constate qu’en France, les usines sont particulièrement vieillissantes. Or la gamme de capteurs connectés développée par Henkel et reposant sur l’IIoT (Internet industriel des objets) permet de les laisser suivre les équipements difficiles à inspecter, tels que les tuyaux, les purgeurs de vapeurs ou encore les valves qui sont cachés sous l’isolation et demeurent difficiles d’accès – nécessitant parfois de monter sur un échafaudage pour aller inspecter des équipements : cela prend du temps et implique d’occuper inutilement les maintenanciers alors qu’ils seraient plus utiles sur des opérations plus routinières.
Qu’apporte concrètement Henkel à travers ces nouvelles familles de capteurs ?
Les capteurs répondent à de nombreux défis, en particulier ceux de la productivité, mais ils permettent aussi de pallier en partie aux problèmes de recrutement ; le « 4.0 » attire en effet davantage les jeunes générations de techniciens et permet aussi aux clients d’être plus « sexy » pour attirer la génération Z, habituée à travailler avec l’IOT.
En matière de technologies connectées, notre gamme âgée de 2 ans est amenée à se développer très vite dans les prochaines années. Nos solutions de capteurs digitaux (dont je suis responsable) servent à optimiser le fonctionnement des équipements de maintenance sensibles. Sa force réside dans la performance des capteurs mais aussi dans la connexion à l’algorithme LOCTITE Pulse qui informe immédiatement le département maintenance du client qu’un équipement est en mode défaillant. Ces capteurs sont utiles pour la détection de fuites d’hydrocarbures liquides sur les sites pétrochimiques, le stockage et le transport de carburant, ou pour détecter un mauvais fonctionnement sur un purgeur de vapeur ; rappelons qu’un purgeur qui fuit représente des milliers d’euros de perte d’énergie et des tonnes de CO2 dans l’atmosphère, et un purgeur bloqué provoque une baisse de la qualité de la production et des conséquences financières importantes en cas d’arrêt de production.
Enfin, d’ici quelques mois apparaitront des capteurs de fuites sur les valves ainsi que des capteurs de détection de mauvais fonctionnement sur les échangeurs de chaleur ou les pompes… À terme, la gamme des capteurs couvrira 100% des équipements de maintenance statiques (purgeurs/valves) et rotatifs (pompes...).
Un autre sujet de prédilection pour Henkel semble être aussi le développement durable. Que représente-t-il au sein du groupe ?
David Mouginot
Sur les équipements défaillants, se pose de plus en plus la question de savoir s’il faut réparer ou remplacer. Surtout, nous avons élargi notre savoir-faire dans le domaine de la réparation de surface et de la protection. Ainsi, avec le récent rachat de Critica Infrastructure, nous proposons désormais des solutions complètes de haute technicité pour la réparation et la remise en état des infrastructures critiques au sein des industries du pétrole et du gaz, du raffinage, de la chimie, de la métallurgie ou encore dans l'approvisionnement de l’eau. Ces composites, enduits d’une résine, permettent ainsi d’augmenter de deux à vingt ans la durée de vie des tuyaux et des réservoirs. Nos solutions de réparation par composite (renfort de tuyaux par exemple) ou de renforcement structurel, permettent de réparer sans arrêt des opérations chez le client et ne pas remplacer leurs équipements – ce qui implique moins d’émissions de CO2 et moins d’impact sur la production des clients.
Car notre but est clair pour les prochaines années : apporter ces solutions innovantes dans la maintenance afin d’optimiser au maximum l’utilisation des machines (priorité des responsables maintenance) et d’impacter positivement l’avenir avec des solutions répondant aux exigences de « sustainability », à savoir : moins d’arrêt machine, moins d’émissions de CO2, tout en augmentant la sécurité des sites et du personnel et en réduisant l’impact environnemental avec la baisse de façon sensible de la consommation énergétique des usines.