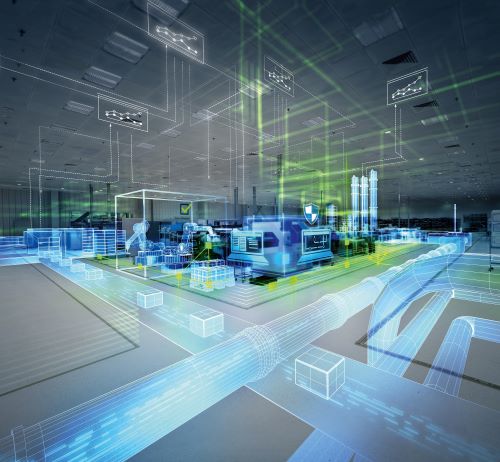
L’intelligence artificielle (ou « IA ») a le vent en poupe. Mais de quoi parle-t-on exactement ? Car entre machine learning, capteurs intelligents ou technologies « edge », et des machines capables de se gérer seules, en fonction de leur environnement industriel, il y a encore un fossé important. Néanmoins, les technologies progressent et les applications se multiplient.
Les technologies dites « du futur » ou « d'industrie 4.0 » sont aujourd’hui une réalité. Désormais, au-delà du MtoM (communication de machine à machine), de la gestion informatique de la maintenance (GMAO) ou de la production avec le pilotage du process et des machines en automatique ou à distance, les équipements seront amenés à communiquer entre eux et à interagir de façon plus pertinente… pour ne pas dire « intelligente » ; l'intelligence restant du ressort de l'humain dont la tâche sera davantage d'intervenir en amont au moment de programmer ces différents systèmes en fonction d'objectifs de pannes, de productivité ou d’économies à atteindre.
Quel intérêt peut présenter l'IA pour la maintenance ? Ne soyons pas dupes. Les grands discours de certains grands groupes disant utiliser de l'intelligence artificielle dans tous leurs services correspondent bien souvent à des discours marketing et à une réalité bien différente. Plus précisément, on parlera de systèmes de capteurs intelligents – dotés de calculateurs – pouvant adapter un process en fonction de paramètres préalablement établis en amont, au mieux capables d'apprendre de leur environnement industriel. Mais cette avancée est déjà considérable.
Quelles applications concrètes ?
Pour mesurer l’efficacité de l’intelligence artificielle dans la maintenance industrielle, quoi de mieux que des exemples concrets d’application. Chez Actemium (groupe Vinci Énergies), on a déjà mis en place un système permettant par exemple de savoir à quel moment il est temps de changer les couteaux d’un coupe-racine. « Une des premières opérations pour la production de sucre est de découper la betterave sucrière avec un équipement appelé un coupe-racine ; or lorsque les couteaux de découpe sont usés, le rendement sucre diminue, souligne Alexandre Maksimovic, responsable Technique Maintenance & Services d'Actemium. Si l’usure des couteaux a un impact sur un des principaux indicateurs de production de l’installation, il est impossible de la mesurer directement dans l’équipement. » Pour ce faire, Actemium AES Veghel a développé un modèle de prévision indiquant le moment recommandé pour le changement des couteaux.
Concrètement, il est impossible d’instrumenter directement les couteaux du coupe-racine pour mesurer leur usure. La technique a donc consisté à exploiter toutes les informations existantes et collectées depuis des années tant du côté de l’exploitation que celui de la GMAO pour l’enregistrement des opérations de remplacement des couteaux. Un modèle mathématique d’usure des couteaux a ainsi été établi à partir de ces différentes sources de données en utilisant des algorithmes d’optimisation bien connus en data science : méthode d'escalade, algorithme du gradient, algorithme de colonies de fourmis et aussi réseaux de neurones.
Mais, les données initiales n’étaient pas optimales et adaptées à l’objectif d’estimer l’usure des couteaux. « Par conséquent, notre modèle souffrait évidemment d’une mauvaise qualité de prévision, précise Alexandre Maksimovic. L’idée a donc été de créer une interface spécifique pour les opérateurs de l’installation qui leur permettait de confirmer ou pas les prévisions de l’algorithme et ainsi de les améliorer ». Cet assistant intelligent a permis d’éviter les remplacements trop précoces des couteaux et de garantir l’efficacité de la découpe des betteraves sucrières qui optimise le rendement sucre. Cet exemple de réalisation est intéressant car toutes les données collectées depuis des années mais n’étaient pas utilisées.
Même approche mais autre exemple, l’automatisation du démarrage d’une installation de production de lait. Ce type d’installations sont composées de réseau de tuyauteries complexes avec des réservoirs tampon positionnés régulièrement dans le circuit. Démarrer une telle installation et ne pas mélanger les lots de production est une gageure pour l’exploitant. « Les modèles de prévision permettent d’anticiper les vidages des circuits et des réservoirs ; il s’agit d’une solution éminemment efficace pour déterminer le bon moment pour déclencher l’introduction du nouveau lot de production. Sans de tels modèles de prédiction, chaque panne technique conduirait à des pertes importantes de production et d’énergie », comme en témoigne une réalisation d’Actemium Beverage Aalter.
Si de gros efforts restent encore à fournir pour convaincre les industriels et les professionnels de la maintenance, notamment dans l’accès à de telles technologies qui nécessitent de recruter des « data-scientists », les applications se multiplient… tant que celles-ci répondent aux besoins concrets de la maintenance industrielle.