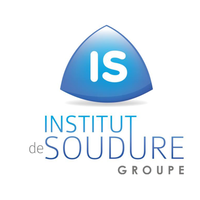
Face aux importants coûts liés aux arrêts de production d'équipements sous pression, mais aussi et surtout pour éviter tout risque d'accidents causés par des défaillances, d'avaries ou d'usures, il existe des solutions permettant de mieux surveiller et déterminer des courbes de vieillissement. Le point avec deux spécialistes issus du groupe Institut de Soudure.
Bien connu du monde industriel, l’Institut de Soudure se définit comme un expert du soudage mais aussi des matériaux, allant de la caractérisation au contrôle destructif et non destructif de pièces ou d’installations. Dans ce cadre, et répondre aux problèmes d'endommagement de pièces (dans tous secteurs industriels à l'exemple du nucléaire, de l’oil & gas ou encore de l’aéronautique), le groupe dispose d'une activité appelée « E3C » (pour Expertise, Calcul Conception et Conseils).
Plus précisément, ce laboratoire travaille autour de deux axes : l’expertise d’une part, le calcul et la conception d’autre part. « En matière d’expertise, nous sommes confrontés aux problématiques d’avarie de pièces suite à un problème identifié sur le site ou directement sur une pièce que nous recevons à Villepinte. Le but est d’expliquer et d’identifier les causes d’endommagement (corrosion, fissuration) d’une pièce ou d’un échantillon comme un morceau de tuyau », détaille Nicolas Gozdecki, responsable de l'activité E3C d'Institut de Soudure. « Plus globalement, notre objectif est de soutenir les industriels sur des aspects liés aux endommagements et au contrôle des installations ».
Cette activité d’expertise s’effectue à travers un panel de moyens de mesure afin de déterminer si la cause d’endommagement est liée au matériau lui-même ou s’il s’agit d’un problème issu du fournisseur voire d’une erreur humaine. « À partir de prélèvement effectué en laboratoire, on observe au microscope binoculaire, optique et par balayage afin d’observer les ruptures et en tirer des conclusions sur la propagation de la fissure, explique Nicolas Gozdecki. Il est également possible d’intervenir sur le site du client via une méthode de la réplique métallurgique : on prépare la surface de la pièce et on y dépose un film pour récupérer l’empreinte qu'on analyse ensuite en laboratoire. »
Quant au second axe de l'activité E3C (calcul et conception), il est complémentaire de l’expertise. Il s’agit d’un appui permettant, sur des équipements neufs ou déjà en service, de déterminer les causes des avaries prévues ou non et de déterminer si l’on peut vivre ou non avec ce défaut sur l’équipement. « Grâce à cet appui de l’expertise, nous sommes en mesure d’identifier le phénomène de dégradation et évaluer la nocivité de ses défauts (selon une approche « FFS » – Fitness For Services conduite selon des codes d’aptitude à l’emploi tels que l’API579 ou le BS7910. Cette démarche s’inscrit dans le cadre du code de construction d’origine, à titre d’exemple le CODAP, un code de construction dont le but est de fournir des règles communes aux fabricants d’équipements sous-pression) », souligne Ménouar Houari.
Objectif ? Délivrer le niveau d’aptitude à l’emploi de l’équipement. Ensuite, grâce au calcul numérique, il est possible de déterminer la durée de vie résiduelle des équipements et de proposer, le cas échéant, des conseils ou des solutions afin de renforcer ou réparer les parties endommagées.
Les équipements sous pression en ligne de mire
Qu’il s’agisse de silos à grains ou à sucre, d’échangeurs, de réacteurs ou de chaudières, les équipements contenant un gaz sous pression présentent des dangers particulièrement élevés d’accident aux impacts à la fois humains, environnementaux et économiques.
C’est pourquoi, il est essentiel de déterminer des modes de dégradation selon les situations de chargements ; dans tous les cas, il faut que la matière (comme l’acier par exemple) soit en capacité de résister aux risques de détérioration pouvant être provoqués par la fragilisation liée à de l’hydrogène. Il en est de même pour la fatigue ou la corrosion.
Aussi, peuvent apparaître des phénomènes de vieillissement dans le temps qui dégradent naturellement la résistance de la matière. Dans ce cadre, les Codes FFS proposent deux approches : la première est analytique et s'applique surtout sur des équipements « classiques » et de façon préventive. Ce calcul n’est cependant pas élaboré au point d’analyser des cas de défaillances complexes. La seconde approche, dite par éléments finis, consiste en une modélisation numérique de l’équipement. Ce calcul permet cette fois d’étudier les équipements y compris les plus complexes.
En application, citons l’exemple d’un bac de stockage d’ammoniaque évoluant dans un environnement sec. Si on ne contrôle pas l’oxygène, des phénomènes de corrosion et de fissuration sous contraintes peuvent apparaître. S'il est possible de suivre par calcul ces phénomènes de fissurations, ce n'est pas le cas de certains modes de dégradation telle que la corrosion, car une fois en service, l’équipement est déjà sous pression et le protocole de surveillance se révèle particulièrement compliqué. Autre exemple, un bac de stockage à toit fixe renfermant une poche de gaz présente des risques d’explosion du réservoir. Le réservoir doit être frangible en favorisant une rupture du toit. Il est donc indispensable de suivre l’état de dégradation en service et de surveiller l’évolution du risque de ruine du bac.
« Pour suivre les courbes de vieillissement, il est possible de mettre en œuvre un monitoring par contrôle non destructif à l'aide de capteurs positionnés sur l’équipement pour contrôler les fissures, précise Menouar Houari. Aussi, si ce type de moyen de contrôle se révèle limité, il est également possible d’effectuer une analyse par émissions acoustiques. Mais cela reste difficile à mettre en place. Dans ce cas, il est préférable de définir des rondes d’inspection plus fréquente que les décennales ou les quinquennales préconisées par les constructeurs ».
En cas de problème, si un dommage ou une avarie apparaît, et pour laquelle l’exploitant ne possède pas les compétences en interne, il a la possibilité de solliciter des établissements comme l’Institut de Soudure. Ce type de structure sera en mesure de mettre en œuvre plusieurs compétences à travers deux étapes : les conditions de dimensionnement et les risques liés à l’endommagement de manière à comprendre la nature du phénomène. Puis l’expertise et la méthode d’analyse par réplique permettront d’orienter vers une réparation ou envisager la possibilité de continuer à fonctionner en l’état. « Mais il est difficile d’expliquer un dommage par un calcul. Dans la mesure où on n’a jamais vraiment tous les éléments en main, celui-ci s’avère parfois insuffisant. Notre mission est donc d’affiner cette recherche et d'apporter des solutions, de réparation ou de remplacement de l’équipement ».